New Technology for Silicon Nitride Composites
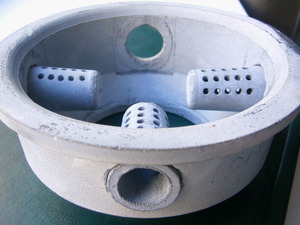
“At the beginning, we mix silicon powder with molten paraffin. We add abrasive grit of silicon carbide or aluminum oxide as a reinforcing component for this dispersed mixture. The mixture is cast into a pre-fabricated metal mold at 70 degree Celsius and at no more than 5 atmospheres of pressure,”– Sergey Sitnikov, an engineer from Department №903 explained,–“
After casting, the paraffin stiffens and its percentage does not exceed 12-25%. Then we do two staged thermal treatment; firstly we heat the part, placed into special powder-adsorbent, up to 180 degree Celsius, at the second stage – on air up to 500 degree Celsius. This treatment allows removing all the paraffin from the raw part.
Finally, it is heated to the temperature between 1300 °C and 1400 °C in a nitrogen environment for getting the desired material.”
Before molding, the silicon powder with the purity of 99% is put into the vibratory ball mill SVM-2 for grinding for several hours by 30 kilos of steel balls. The grinding quality is controlled by The Acoustic & Electro-acoustic Spectrometer DT-1202, a device for measuring particle size and zeta potential in concentrated dispersions and emulsions with particles concentration from 1 to 50 weight percent.“The particles do not sediment due to electric double layer at its surface,”– Sergey Sitnikov said,–“We add surfactants to the mixture for helping particles to get an electric charge. Charged particles repel each other and hence uniformly fill the space.”
The Acoustic & Electro-acoustic Spectrometer DT-1202 sends ultrasound through a container with a test substance and evaluates the attenuation of the signal for measuring particle size.
Also, the device evaluates the surfactant concentration to improve the stability of the desired dispersion.
The dispersion stability can be assessed by measuring zeta potential, a parameter characterizing electrochemical equilibrium on interfaces. Particles with the zeta potential value greater than 30 mV do not sediment.Generally, the silicon nitride composites can be used for manufacturing various parts and assemblies for mechanical engineering, aerospace engineering, and the chemical industry.In addition to the hot-casting technology described above, MAI scientists explore other methods for raw parts molding like electrophoretic deposition or additive modeling.
Two new prototypes of 3D printers aimed at working with silicon mixtures are under design at Faculty of Applied Mechanics. First one is based on Binder Jetting technology. The second one – on FDM technology. Scientists plan to use these printers for manufacturing the parts with ultimate geometrical complexity. Department № 903 “Materials Science” and Department №904 “Technical Drawing” are involved in the works.
Development of the 3D printer based on Binder Jetting technology is financed by the Special Federal Programme № 1.3.
“The first results have greatly inspired us. We plan to develop a technology for manufacturing parts for spacecraft in the near future,” – Sergey Sitnikov said.
He assumes that the technology for the serial production of parts from silicon nitride composites exists neither in Russian nor in the world yet and hopes that Moscow Aviation Institute will be the first place wh ere such technology will be invented.