MAI came up with a technology for extra strong drone wing creation
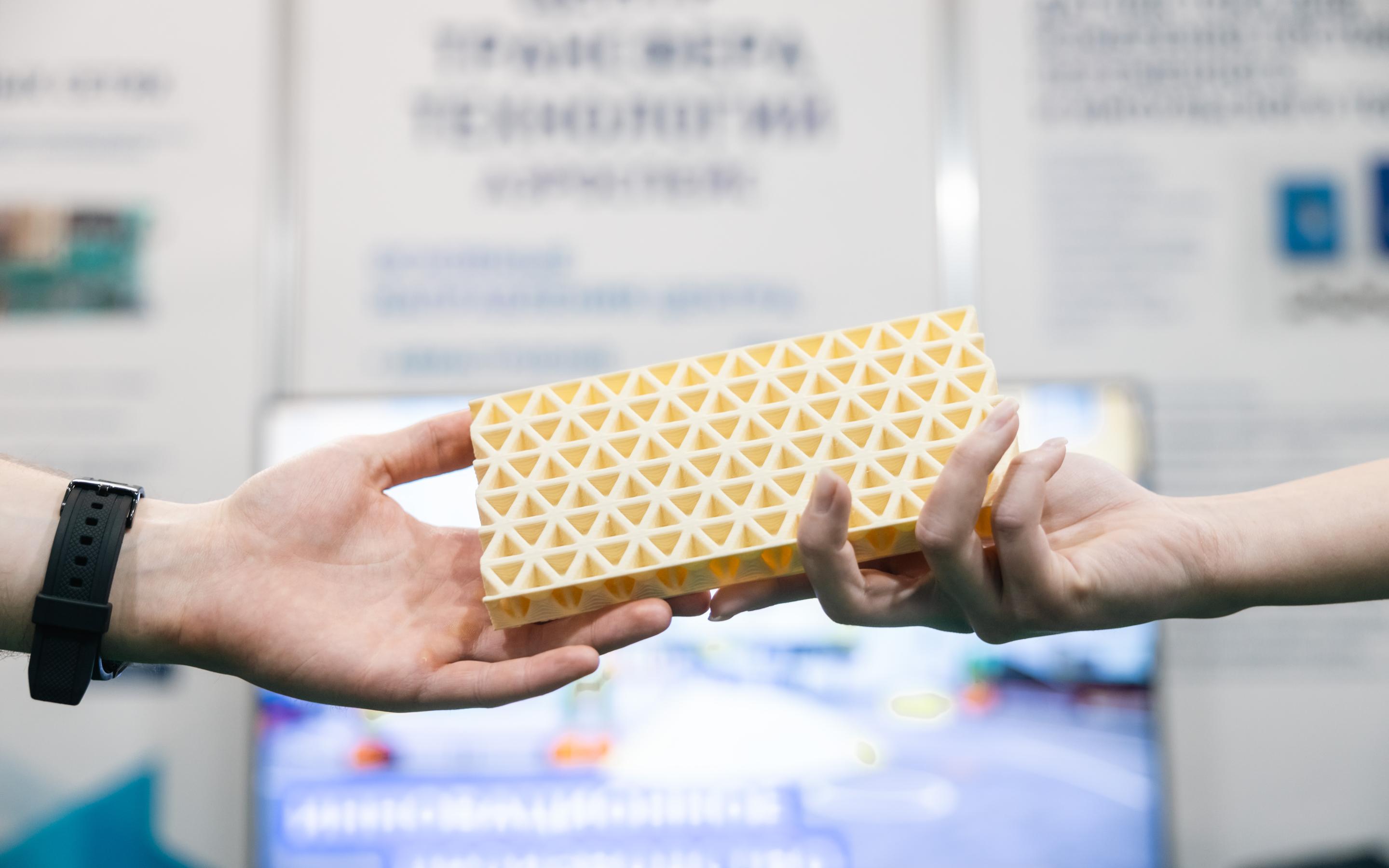
Experts of Moscow Aviation Institute applied the technology of manufacturing food containers in the production of a special aviation material – prefabricated cellular filler. The development might replace traditional honeycomb cores, which are now widely used in the aviation industry.
Production speed
Moscow Aviation Institute patented a new filler for the wing of unmanned aerial vehicles (UAVs). The development is easy to manufacture and has high strength characteristics. The material is cellular panels connected in layers. The layers mutually reinforce each other. The edges of the cells also increase the rigidity. In addition to the filler itself, scientists protected the technology of its manufacture and the assembly of the UAV wing from a new material with patents. This development can be used as a connecting link in the manufacture of three-layer wing skins for drones.
In addition to the filler itself, scientists protected the technology of its manufacture and the assembly of the UAV wing from a new material with patents. This development can be used as a connecting link in the manufacture of three-layer wing skins for drones.
– The speed of aggregate production is one of the main advantages of the technology. It is possible to do that by stamping or molding. Such methods are used for ultra-fast mass production of various products. For example, in the laboratory, the production of one panel using this technology took only two minutes, – Andrey Kolpakov, co-author of the development, researcher of Institute No. 1 “Aviation Technology”, told Izvestia.
Today, three-layer skins are widely used in the aircraft industry. They consist of two outer layers, between which a lightweight aggregate is placed. As the latter, materials of a honeycomb, porous or corrugated structure are often used.
– The outer layers traditionally carry out the main load when creating the lifting force of the wing. Fillers play the role of a connecting element, which ensures the stability of the system. Therefore, they usually have low strength, – Andrey Kolpakov explained. – In our case, honeycomb panels themselves hold their shape well and can take on the role of the main load-bearing element. In this case, it is possible to reduce the weight of the skin.
The aircraft designer noted that the number and shape of the cells, as well as the thickness of the panels, might be different depending on the given performance characteristics of the aircraft. To select the filler parameters, scientists use their own automated software package. It allows to calculate the cellular structure superimposed on a complex geometric shape, taking into account the double curvature and variable thickness of the structure.
Without sacrificing the strength
According to the developers, this allows the use of materials with lower strength characteristics for the filler, which were previously considered non-typical for aviation. For example, various types of plastics.
– As an experiment, we made honeycomb panels by vacuum extrusion from sheet plastic. It is used for the production of food packaging. Surprisingly, a product made of waste “non-aviation” material turned out to be more durable and reliable compared to a honeycomb structure,” Andrey Kolpakov noted.
According to the scientist, the cellular structure allows to reduce the consumption of resources. This will reduce the weight of the aircraft and reduce the costs of production and operation.
Another advantage of the new filler is the ability to make local changes to the wing structure without sacrificing strength. For example, for the purpose of laying wiring, pipelines and installing the necessary equipment.
Also, the cellular structure stops local damage, preventing them from progressing and destroying the empennage of the aircraft.
– A well-known problem in the aircraft industry is the condensate inside the wing. It leads to the reduction of the life term of the aircraft. In our development, there are communicating cavities inside. As a result, the condensate is removed naturally, – Andrey Kolpakov shared.
Not only drones
In the future, the development can be used in other industries, experts from Moscow Aviation Institute believe.
In particular, cellular filler can be used to facilitate building cladding structures and interior floors. The scientists also worked out the option of using the technology in the manufacture of the roof of a car body. This will make it possible to lighten the upper part of the cars and increase their stability on the roads.
– The development of domestic technologies that increase the speed of assembly and reduce the cost of products, under the current conditions, is a priority direction for development for any Russian company,” commented Oleg Fomenko, General Director of KB Rus, which develops copter-type UAVs, on the invention.
According to the expert, the MAI technology has prospects, but it is important to work out the technology in relation to specific aircraft.
– For the wing of small UAVs, foamed fillers based on polymers or classic honeycomb structures are used more often. For large ones – a power set, from ribs and spars (longitudinal and transverse elements in the wing structure. – Izvestia), – explained the head of the laboratory "Digital Technologies for the Production of Products from Polymer and Composite Materials" of the Irkutsk National Research Technical University Yury Ivanov.
He added that cellular fillers could find their niche in production of simple and cheap long-range devices. Especially those who do not need to go back.
– In modern UAV production facilities, automated cutting of semi-finished products is used. In this case, the molding of products is often done manually. The use of cellular fillers will significantly reduce the time of manufacturing products. They also have increased rigidity and strength, which will significantly increase the resource of products. This will increase the payload of the devices, – says Vadim Istomin, Leading Engineer of the Competence Center of the National Technology Initiative “Digital Materials Science” based at Moscow State Technical University.
The specialist explained that one of the obstacles to the widespread use of the new technology may be the need to significantly upgrade the equipment at the plants.
MAI scientists note that they are ready to test the technology. To do this, it is necessary that the potential customer decide on the optimal configuration of an unmanned vehicle and provide the performance characteristics. Based on this information, the designers will make a prototype for testing and research. As a result, it will be possible to calculate the efficiency of the development.