MAI scientists are developing the effective sensor for hydrogen leakage detection
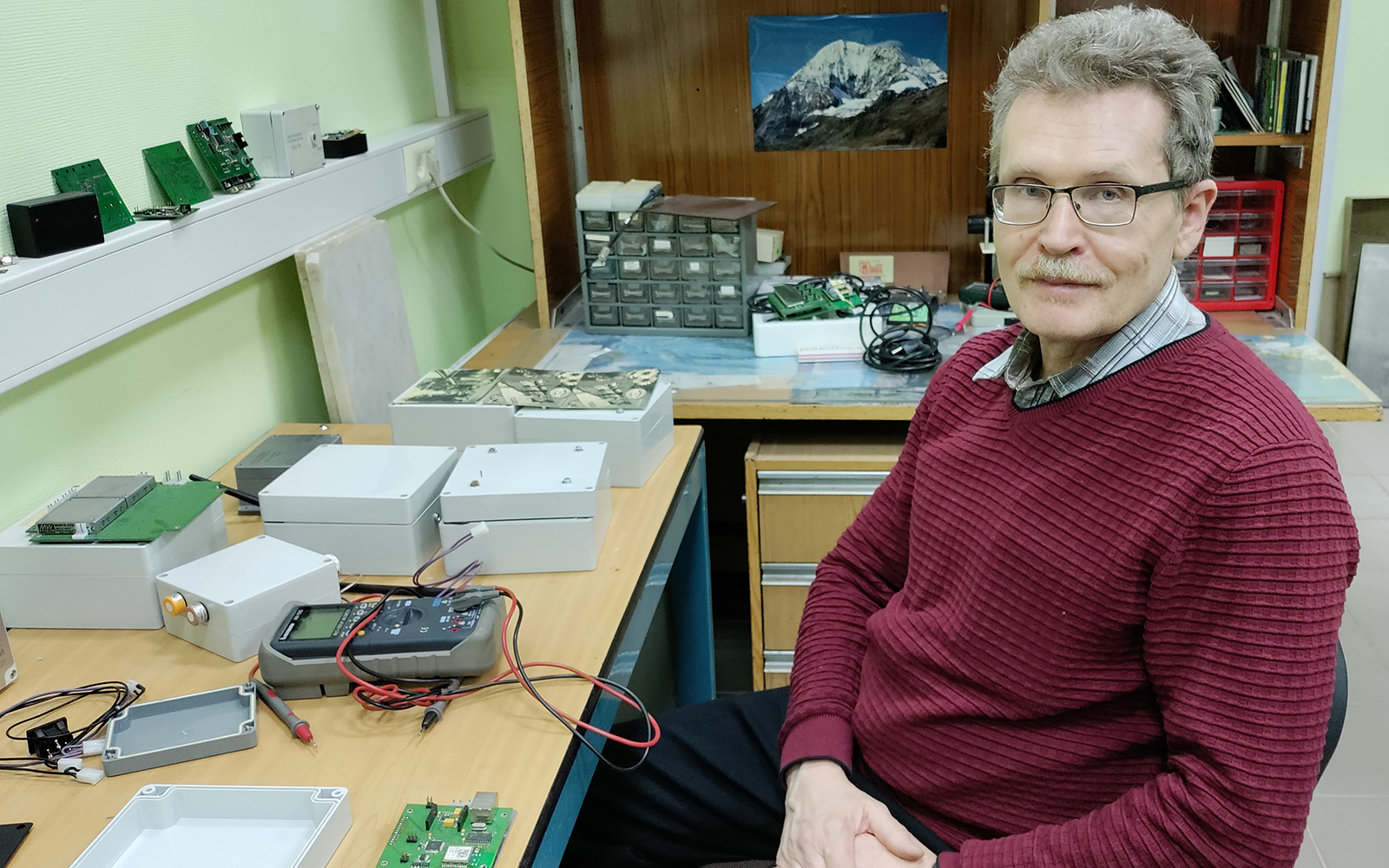
Before starting the discussion about the peculiarities of the hydrogen sensor being developed by MAI scientists, it is necessary to emphasize the importance of hydrogen as the energy source in the modern world, especially taking into consideration the global carbon neutrality course taken by the technologies that are now developing in Russia and worldwide.
Mankind is aimed at transition to environmentally friendly types of energy. And hydrogen the source of energy that looks like it has prospective. It will certainly push coal, fuel oil, diesel fuel, gasoline and natural gas aside.
H2 consumption has been growing recently and it will only continue to increase during the upcoming decades. The policy of achieving carbon neutrality, that is, the rejection of carbon dioxide emissions into the atmosphere, is the exact main reason for that.
More specifically, we can foresee the emergence of a large number of thermal power plants operating on hydrogen. The efficiency of such a station will reach 60%. Approximately the same good indicator is given by the current gas-fired thermal power plants operating on methane, but hydrogen has a number of advantages.
First of all, it has the highest thermal conductivity among all gaseous substances and, which is extremely important, it allows to regulate the operation of gas turbines easily, and, respectively, change the output power quickly. At nuclear power plants, for example, it is absolutely impossible to do this in a short period of time. Hydroelectric power stations are more flexible in terms of capacity change, but a number of places where it is allowed to build them is restricted.
Hydrogen thermal power plants are very convenient to use when the volume of consumption changes dramatically. Perhaps hydrogen power plants and the energy potential of H2 are of high importance for European countries, for they are trying to use renewable energy sources (RES) as widely as possible, but have difficulties in ensuring the energy balance in cloudy weather and during periods when there is no wind.
As the hydrogen revolution is obviously at its dawn, our country also has certain ambitions. Almost all newly built pipelines, including Nord Stream 2, are made using materials and technologies that allow H2 to be pumped. Russia could hypothetically become the major global producer and exporter of hydrogen.
Though, it is still better to mix "transit" hydrogen with other substances, for example, with methane – for safety reasons. At the outlet of the pipe to the territory of the consuming country, this mixture will be separated into two gases. And for export purposes, the easiest way would be to use the underwater pipeline, because for pumping through the land artery, you will inevitably have to create a fairly extensive infrastructure for pumping and servicing.
Broad prospects are opening up for hydrogen in the automotive technology segment. This trend has also affected our country. It is known that in the near future in Moscow it is planned to create an extensive fleet of hydrogen electric buses.
However, as far as I understand, ambitious plans for a larger use of hydrogen as the energy source are constrained by the safety factor?
That is not the only restriction. A number of issues regarding the choice of the most optimal methods of hydrogen production have not been resolved yet. There is a so-called green hydrogen, which is extracted from water via electrolysis. In this case, no CO2 emissions are generated, but this method is energy intensive and quite costly. There is blue hydrogen – it is extracted from methane, but CO2 is evolved.
As far as security is concerned – on the one hand, in any case, this issue must be taken very seriously, on the other hand, the risks of mass use of hydrogen should not be exaggerated. For example, the industry that has long used hydrogen as an element for chemical reactions has, in essence, solved safety issues.
There are certain security gaps in new sectors of industry that are specifically aimed at using H2 as an energy source. In everyday life, and at all, as I think, hydrogen will not be used soon.
Of course, when talking about the attractiveness and future expansion of hydrogen applications, it is impossible to ignore its shortcomings, which most directly affect safety.
The first one is the storage complexity. H2 has the ability to penetrate even through hard surfaces. Its spread is restrained only by a shell made of metals, and even not all of them.
The second one is the flammability, the limit of which is much wider than that of hydrocarbons and methane. The concentration of H2 in the environment must be between 4 and 75% for an explosion to occur. For comparison: for methane, this range is much narrower – from 4 to 15%.
Actually, for this reason, it is important to conduct accurate and timely measurements of the H2 concentration. What are the problems of modern hydrogen level sensors? Why did MAI decide to create a new one?
Currently, in Russia and abroad, sensors that are focused on the determination of the concentration of various combustible gases and vapors are widely used. They have both advantages and disadvantages. The approach of the AHP team is to use a selective sensor that measures only H2 and does not sense other gases.
Creating a sensor that detects (determines) only hydrogen from a variety of mixtures of other substances is a very difficult task. But, from our point of view, such a product is necessary and in demand, since it will be much better to take into account the most important properties of hydrogen: its fluidity, explosiveness, combustion temperature.
What does such a sensor look like?
Our sensor is compact and it will fit in a housing less than one cubic centimeter. The actual size is smaller, and the "sensitive" part of the sensor is quite small – it is a spiral about 0.5 mm long and about 0.3 mm in diameter.
It is not used separately, it is one of the components of the equipment of ready-made measuring devices, in our case it is a gas analyzer. In order to easily integrate our sensor into the gas analyzer, a standard housing with a diameter of 8 mm and a height of 10 mm was chosen.
In fact, we could make the sensor even more compact, but there is no point in that yet, since it needs to be built into standard gas analyzers.
And who exactly is working on this sensor?
The group of postgraduate students, employees and graduates of MAI Radioelectronics, Telecommunications and Nanotechnologies Department of Institute No. 12 Aerospace Science-Intensive Technologies and Production is working on the project. I am the leader of the group.Last year, our project became the winner of the competition for grants from the Russian Science Foundation in "Fundamental scientific research and exploratory scientific research by small individual scientific groups."
What are other features of the sensor that your group is working on?
Our sensor belongs to the type of thermal catalytic sensors. In addition to this class of sensors, there are electrochemical, semiconductor and optical. Due to a number of features, they cannot detect hydrogen with high efficiency.
For example, electrochemical and semiconductor sensors capture hydrogen concentrations that are “harmless” from the point of view of explosiveness and, on the contrary, often “choke” – lose their sensitivity when the H2 level approaches a truly threatening threshold.
In this respect, thermal catalytic products stand out if compared with other types of sensors. They are the most suitable for measuring hydrogen in air in the range from 0.1 to 2% and higher, which most effectively helps to prevent explosive situations.
The essence of the operation of a thermal catalytic sensor is that hydrogen penetrates through the sensor membrane, behind which a sensitive element heated by current is placed. This element, in turn, has a surface coated with a catalyst.
It is necessary to heat the gas in order to cause a chemical reaction and thus detect hydrogen. Heating is precisely the principle of operation of a thermal catalytic sensor. Without a catalyst, the temperature of about 900 °C is required, and with a platinum catalyst, which is now widely used – about 300-400 °C.
The problem with modern thermal catalytic sensors is that at such high temperatures it is difficult to completely eliminate the possibility of situations when, during a short circuit and other malfunctions, a reaction occurs that can provoke an explosion.
It will be much safer, if the heating temperature could be lowered significantly. Today, the most advanced sensors give results at 200°C. Our task is to further reduce the temperature of hydrogen measurement.
The strategic goal of the MAI project is to conduct selective measurements of hydrogen in air or in mixtures with other combustible gases at temperatures close to room temperature. In addition to improving safety, it will be possible to reduce energy consumption. As a result, the battery life of the sensor will increase.
There is no point in lowering the operating temperature to room temperature. A good result, from our point of view, would be a product that functions when heated to 60-70 °C. Last year we developed a catalyst that operates at just over 100°C, but now we are close to making a better sensor.
The catalysts in current gas sensors are platinum group metals, but not all of them have previously been used to monitor hydrogen. We use iridium (Ir) and rhodium (Rh) in its pure form, or mixed with platinum (Pt) and palladium (Pd).
This combination of materials should improve the parameters and performance of our thermal catalytic sensor. This is a fairly low operating temperature, low power consumption, selectivity, sensitivity, reduced response time (reaction to hydrogen), long-term stability of operation.
The body of the product will be explosion-proof. If, nevertheless, there is a sharp increase in the concentration of hydrogen, a short circuit or another incident, then it will prevent detonation.
When do you plan to complete the project and what plans does the MAI team have for the production of the sensor?
The work will be continued this year, and it is to be completed in 2023. The results that we will obtain during the implementation of the project are of great importance from the point of view of the development and optimization of the parameters of thermal catalytic hydrogen sensors. They will also expand the range of their practical application to new promising areas.
If we talk directly about the plans for the sensor, then, of course, we are sure that it will find its application in finished products. Currently, we are closely cooperating with the Scientific and Technical Center for Measuring Gas-Sensing Sensors named after E.F. Karpov, which is engaged in the production and supply of sensors that detect combustible gases – primarily methane and propane-butane.
Thus, our calculation is that this enterprise will expand its field of activity by offering customers end products that can effectively detect hydrogen.
Naturally, we expect interest from other equipment manufacturers. The market of gas sensors does not stand still, it is constantly developing and growing.