MAI researchers create digital model of heat protection for hypersonic speed
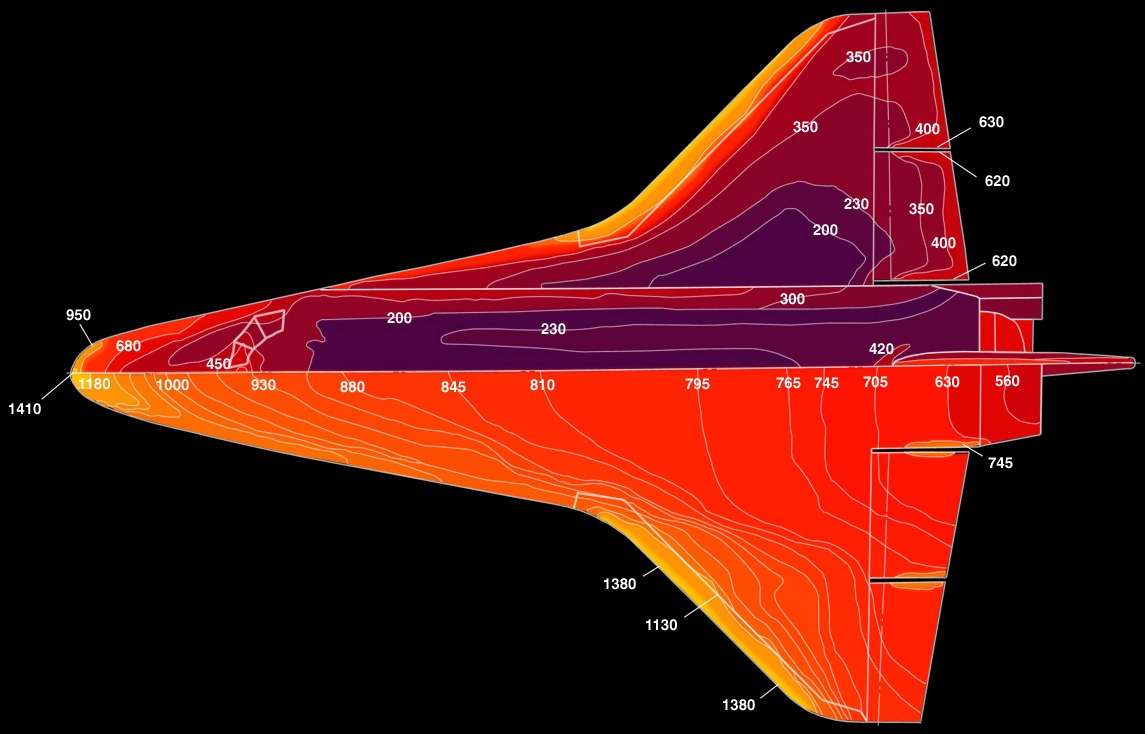
"Within the framework of the project, we are developing complex mechanical and mathematical models for the stress-strain state of composite materials, both structural and thermal protection, under joint force and thermal impact during aerodynamic heating of hypersonic aircraft (FV). We are also investigating the degradation processes of mechanical and thermal properties of composite materials", says Vladimir Formalyov.
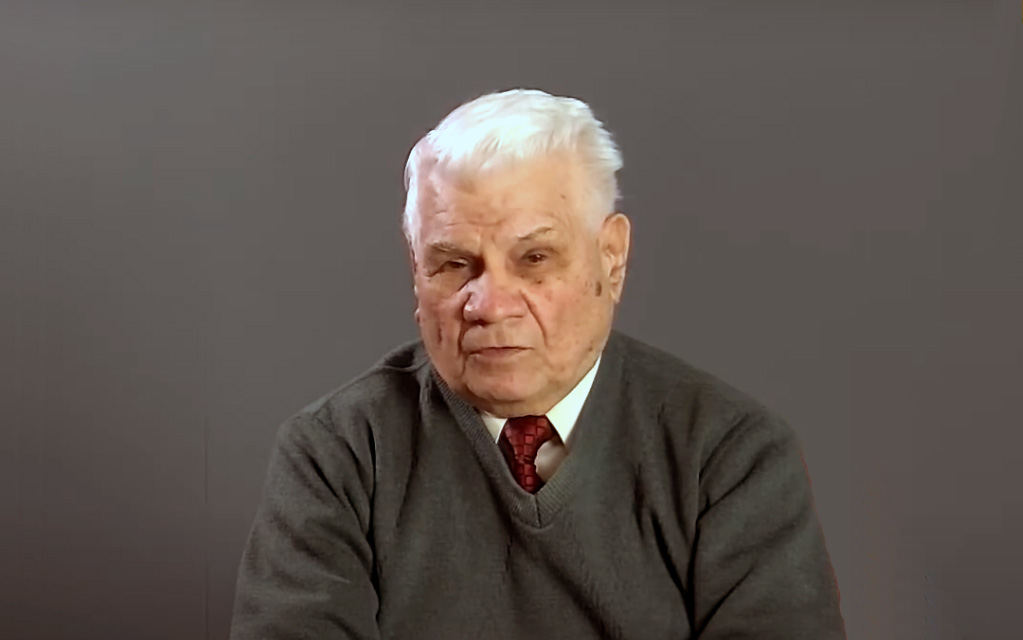
"At the moment, a significant number of structural and heat-protective composite materials with various fillers (silicon, carbon, asbestos, aluminium, titanium, basalt, etc.) with organic and inorganic binders are being developed and introduced into the design practice of power and transport machine building. The key issues in their development and operation are the problems of reliability under high mechanical and gas-dynamic loads, because composites are subject to significant destructive changes, both in the process of alternating cyclic mechanical and high thermal loads, Typical of aerogasdynamic loading of hypersonic aircraft, as the temperature in the shock layer can reach 20,000 degrees on the Kelvin scale "and higher," says Sergey Kolesnik, principal performer of the project, Doctor of Physical and Mathematical Sciences, Professor of Department 806.In 2016, he defended his doctoral thesis on the mathematical modelling of coupled problems of heat and gas dynamics and anisotropic heat conduction under aerogasdynamic heating and inverse heat transfer problems in anisotropic bodies, which gave a significant boost to the project.The project developed a universal law for the decomposition of binders of heat-protective composites at high temperatures. The law is universal as it does not use the poorly formalised chemical kinetics of decomposition. It was derived on the basis of known (passport) values of densities and temperatures of the beginning and end of decomposition of thermal protective composite binders, as well as the exponential nature of decomposition of composite binders.On the basis of this law, a physical and mathematical model of heat and mass transfer in heat-shielding composite materials has been developed that considers binder decomposition, pyrolysis gas filtration, heat and mass transfer, mass entrainment and its effect on the nonstationary temperature field, pyrolysis gas injection into the gas dynamic boundary layer and reduction of heat flow to the outer boundary. Various phenomena leading to significant non-linearity and non-stationarity in mathematical models at high temperatures, such as radiation, the dependence of the thermophysical characteristics of materials on their rupture temperature, anisotropy and multidimensional heat propagation, are also taken into account.
"The formulated problems in each individual area of the investigated problem (prediction of composite properties, determination of temperature fields in heat-proof material under mass entrainment conditions, determination of phase composition, estimation of parameters of coupled heat and mass transfer between viscous gas-dynamic flows and anisotropic bodies, inverse problems, obtaining and testing experimental samples of ceramics, metal composites and carbon composites) are new to a great extent, but it is the integrated formulation of the problem that is completely new and unexplored. Some of the results obtained within the project allowed us to assess the degree of "connectedness" of the processes under study and the possibility of their reliable theoretical description "and optimization," says Sergey Kolesnik.
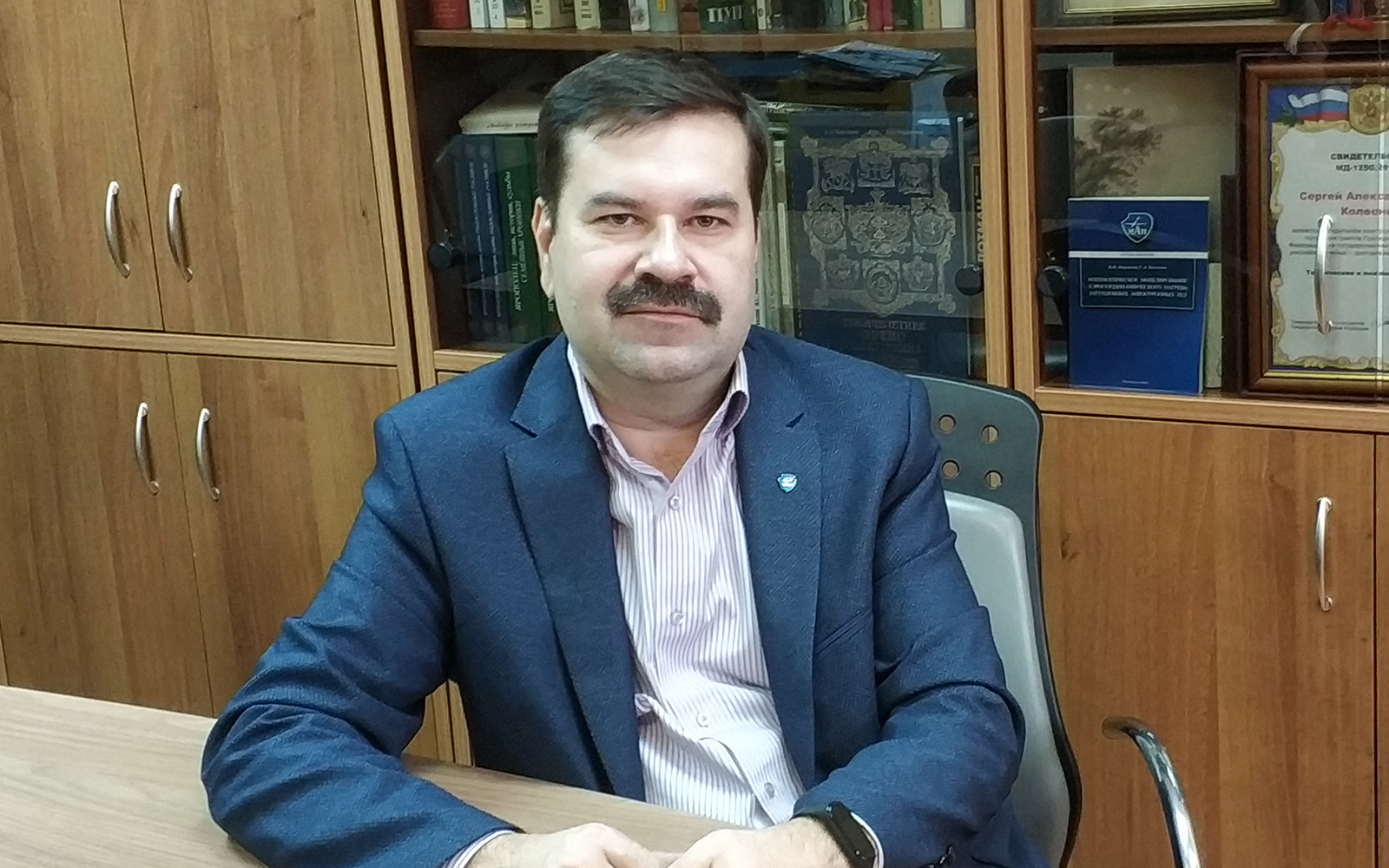