MAI postgraduate student elaborates new 3D metal printing technique
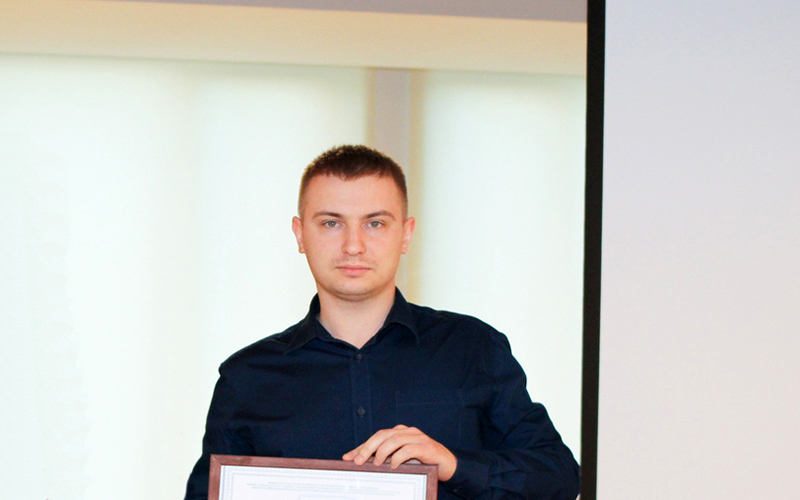
The result of his work will help to produce products with the required characteristics at lower financial and resource costs. The numerical model will also help predict possible manufacturing defects.
Why do you have an interest in research? How and when did you discover it in yourself?
I got enrolled to MAI in 2011. I completed bachelor’s and master’s degrees in the Department 910B "Mechanics of nanostructured materials and systems", and then got a post-graduate job here. I regret that I came to science too late. In my time, the bachelor’s degree was regarded by students more as the first stage of higher education, and almost no one thought about science. Now, as a postgraduate student, I see that MAI is beginning to involve students in scientific activities through various articles and thematic events at the very beginning of their professional career. This is great, because children are immersed in the world of science, directing and setting the appropriate vector.
Today I work in the research Department of the Institute № 9 (NIO-9) and simultaneously conduct educational work with students. Our Department is based on the Institute of applied mechanics of the Russian Academy of Sciences (IPRIM RAS). In the same organization I started my career, entering the master’s program. And it was there that I first met science. First, I was invited to the laboratory to study the effect of barriers on tsunami waves, and then I was transferred to the profile direction — to mechanical testing of rubber samples with the addition of various nanomodifiers. I worked there for two years.
How does MAI help you develop your professional and scientific interests? How was the project idea born and how did it develop further on?
When I entered graduate school, I changed my field of activity and started working on additive technologies. There are still a lot of unexplored aspects in this area, so there is a lot to develop.
The first year of the graduate school is more focused on learning, but by the second year there is enough free time to devote to science. I came to implement the project thanks to my scientific supervisor — Director of the Institute № 9 "General Engineering Training", doctor of physical and mathematical sciences, Professor of MAI Lev Naumovich Rabinsky. He suggested that I develop this topic, since I had collected quite a large pool of developments in this area: publications, author’s certificates for computer programs, and participation in various conferences.
What makes your project unique and innovative?
As part of our work with the additive equipment presented at MAI, we want to develop a new method for printing products of various geometries for the aviation industry and other areas where appropriate technologies are used. Of course, the market is highly competitive. However, the methods that are currently used are based on GOST Standards. We want to step back from them a bit.
The main problem is that today the process of additive printing is very expensive. Our goal is to understand what acceptable values can deviate from the specified requirements in order to get a product with the required characteristics, while reducing financial and resource costs.
The processes occurring in the powder melting chamber at the time of printing are not yet fully understood. Therefore, one of our tasks is to build numerical model of the additive manufacturing process and verify it by conducting full-scale experiments — real printing of prototypes. This is necessary so that in the future it is possible to predict and understand under what conditions, temperatures and sizes of the product "leashes" may occur. Such manufacturing defect can be formed at the end of printing — at the moment when the voltage accumulates and the entire load is removed from the product. The part may lead, and then it will become unusable.
Similar works, of course, were carried out before. But we want to look at this issue from a wider angle.
Do you already know where you will look for potential customers?
We are working on a metal structures printing technique. Therefore, our target audience is not only aviation, but also any other industry that uses additive technologies to create metal parts. There can only be production restrictions. When we manage to achieve the planned result and correctly build the process, I think we will be able to transfer the experience gained to industrial printers. Just now our printer has a smaller scale. We can’t print the engine case on it, but we are able to print some elements already.
What stage is the project at? What are your next steps?
During the first year we made samples and conducted tests on third-party equipment in accordance with GOST in order to get the necessary data for further work. We have also created prototypes of samples that we plan to print in the near future on our equipment, subjecting them to the same mechanical tests. Via using various printing parameters, we want to understand what maximum results can be achieved on our equipment working within the framework of GOST.
Since our work is to study the mechanical characteristics of the resulting products at various printing parameters, we intend to continue to move in this direction.
What personal achievements are you proud of and what plans do you have for the future?
Working at the Moscow Aviation Institute makes it possible to focus on more than one area of research. Now, while additive technologies are trending, I see myself here.
In terms of achievements, it is probably worth noting the number of publications in "Scopus" — I have about ten of them, among which there are publications with the first quartile (Q1), according to the SCIMago Journal Rank (SJR). I am also a co-author in four certificates of registration of rights to computer programs. In 2019 I turned to be the winner of the Council for grants of President of the Russian Federation scholarship of President of the Russian Federation for young scientists and graduate students. And also participation in other grants and promising projects. I am proud to be part of the MAI research team and to be able to develop with the support of strong mentors.