The development of MAI scientist will make aircraft production more cost efficient
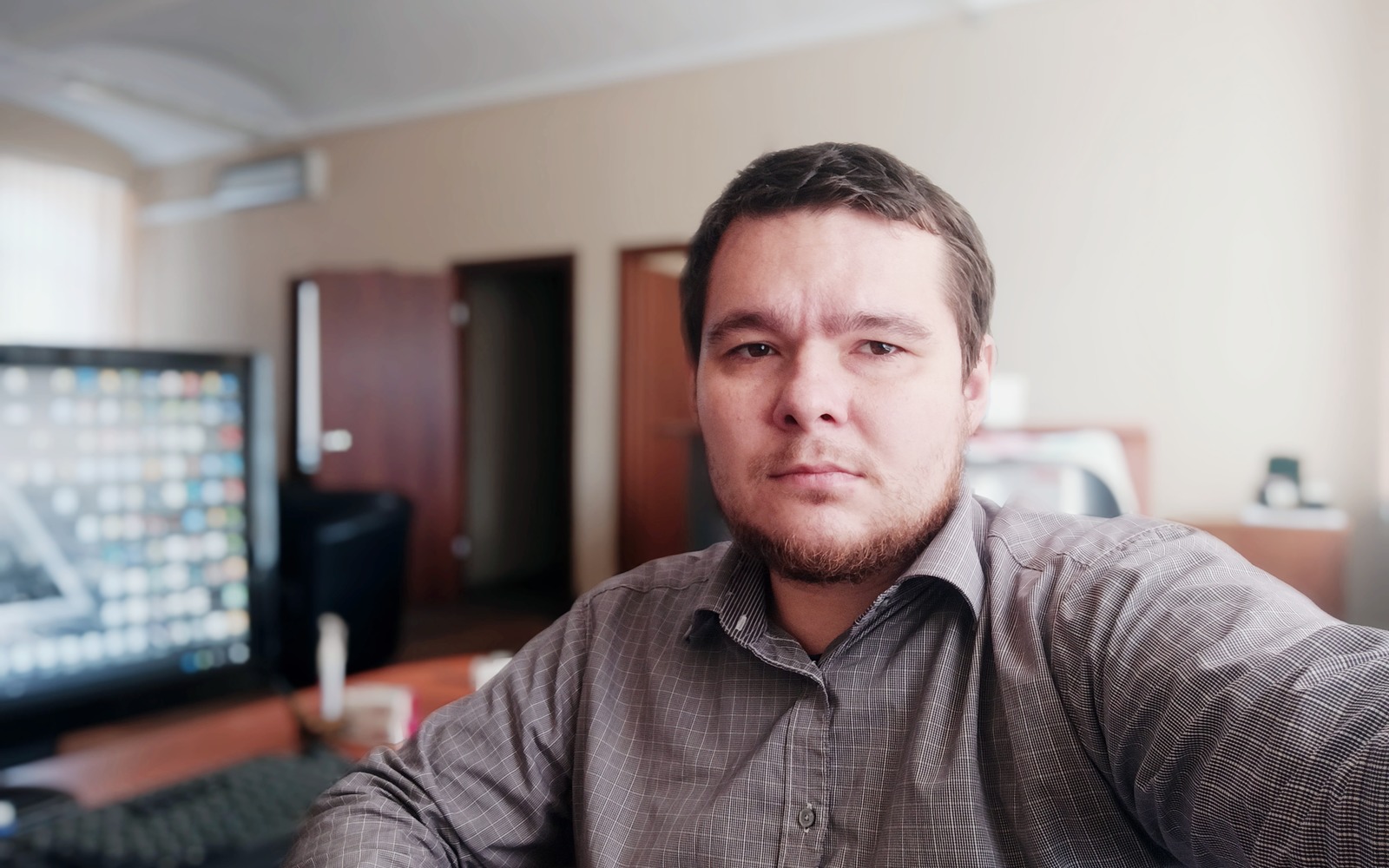
Associate Professor of the Department "Technology of production and operation of aircraft engines" of the Institute № 12 "Aerospace science-intensive technologies and production" of MAI, candidate of technical Sciences Denis Kuritsyn conducts promising research: he creates a methodology for the design and construction of complex tools for friction welding with mixing. This is a relatively new welding method that is used in the production of high-tech products, including aircraft and rocket and space structures.
— In future the technology will allow us to avoid the use of rivet joints in the aircraft industry, -says Denis Kuritsyn. — The principle of metal sheets connection in the solid phase due to plasticization without melting eliminates the risks of disruption of the structural and phase state of high-strength aviation materials that occur during fusion welding. At the same time, the seam strength remains at the level of 95-100% of the initial strength of the material being welded. And also stress concentrators and material integrity violations are excluded, as in the case of rivet connection.
In early 2020 the scientist received grant from the President of the Russian Federation in order to implement his project. This made it possible to perform a number of virtual experiments using "digital double" of a complex-profile tool that takes into account the results of modeling the viscous flow of material in the welding zone, as well as to design optimal processing modes for various materials. In addition, the grant funds made it possible to implement computer projects "in metal": the technology of joining aluminum, titanium and copper alloys of variable thicknesses was developed. The grant allowed to involve other young scientists to scientific work, including Andrey Koreshkov, the post-graduate student of the Department of TECHNICAL and technical research, who made a significant contribution to the development of control programs for robotic equipment.
The new tool will increase the efficiency and reliability of welding due to the formation of high-quality plasticization and mixing of the material in the seam area with no solidification defects, as well as reduce the weight of the finished structure, which is important for the aviation industry. The shape of the tool can be optimized for different materials, thicknesses, and spatial geometry of the weld, taking into account design and technological limitations. This will make it possible to reduce the cost of production processes and provide the aviation and rocket and space industries with high-tech domestic equipment.