The MAI team reached the final of the INRADEL 2020 competition for young scientists
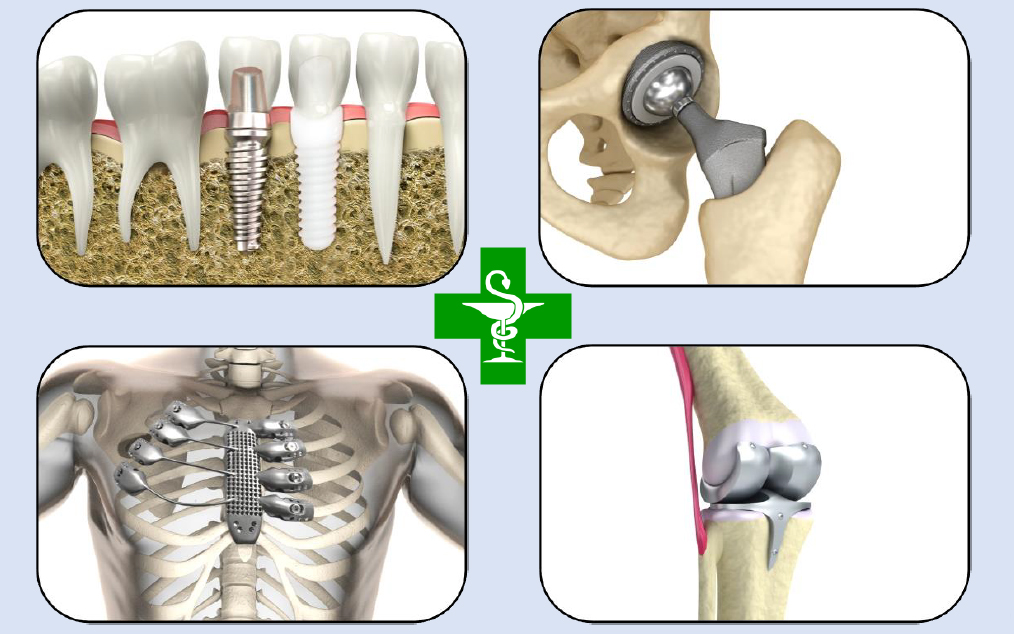
At the end of August, the MAI team reached the final of the INRADEL 2020 competition for young scientists. The event was organized by the "Electronics" Central Research Institute with the support of the Ministry of Industry and Trade of Russian Federation. The competition helps students, postgraduates and young scientists to turn their idea into a high-tech business and build a career in the radio-electronic industry.
According to the results of the expert evaluation, 34 teams from 21 cities of Russia and 42 leading universities of the country were selected for the educational stage, which took place on July 1 — August 23. Only 14 of them made it to the final. Among them there is the ReSurface Team (MAI) with the project "Method of modification of alloys via discharge in a liquid stream". The participants are postgraduate student of the department 902 "Mechanics of materials, dynamics and strength of machines" of the Institute № 9 "Engineering training" Umedjon Gafurov (co-founder, CEO), senior lecturer of the Department 311 "Applied software and mathematical methods" of the Institute № 3 "Сontrol systems, Informatics and power engineering," Sergei Davydov (co-founder, CTO) and senior lecturer 903 "Advanced materials and technologies for the aerospace industry," Institute № 9 Elena Akhmetova (scientific consultant). Now they are recruiting a team of experts in financial analysis, law, HR, PR.
"We have already participated in this competition with another project (medical gas analyzer) in 2019, and won the third prize. We are currently at the stage of negotiations with investors and potential buyers. The new project is at the very initial stage: primary research with further transition to R&D" — says Sergey Davydov.
The competition consists of several stages: initial registration and preparation of the project summary, selection of the most promising projects for training at the technobusiness, and the final stage. The task is to take engineers who are good at their business, but are far away from business, market, consumer, marketing, and to teach them to convert their innovative ideas into real product and sell it profitably.
The MAI team will increase the service life of endoprostheses up to 30-40 years
The project has wide application in two areas: industry and medicine. At the moment they decided to focus on medicine. The essence of the project is to develop an installation for obtaining submicro- and nanostructures on the surface of metals and alloys by modifying them via periodic discharge in a liquid stream. What is that and what problems does it solve?
Nowadays there is a fairly high percent of people who need bone replacement. The problem is that the endoprostheses that are produced on the market today do not have long service life while being simultaneously of a significantly high cost. All this leads to the fact that, for example, after a hip replacement, in approximately 10-15 years, a person needs a revision surgery, which is
"This effect is achieved by processing of the prosthesis in our facility. The sample is placed on a slide table that moves in different directions. On the top there is a tank with the liquid, through which the current is transmitted. At the moment of discharge and contact of the liquid in which various chemical compounds are dissolved with the surface of the processed sample, a micro-explosion occurs, which results in a deep fine modification of the material. This increases the surface microhardness, but preserves the volume properties of the material. And one can process the product of any size." — says Umedjon Gafurov.
At the same time, the opportunity for additional manipulations remains. For example, now the team is working on the possibility of creating hydrophobic (water-repellent) coating on the surface of the product.
"If we talk about the competitive environment, our invention is the leader in all of the abovementioned parameters. The closest methods are the electric pulse and electric spark, but they lack two important elements: there is no possibility of introducing other chemical elements and the processing speed is quite low." — Umejon notes.
As far as the implementation stage is concerned, we have developed a three-dimensional model of the installation, a mathematical model, and a program that will calculate how a particular material will behave. The team is preparing for filing for a patent, and then acquiring the resources, testing of the final installation and execution of technical documentation with subsequent access to the market.
Since the project has a wide range of implementation areas, we plan to focus on the aircraft industry as part of this invention. In the aviation industry, titanium is used often, so the question how to increase the service life and reduce the wear of parts is very acute. The team already got industry representatives from China interested in their work.