MAI for Propulsion Engineering
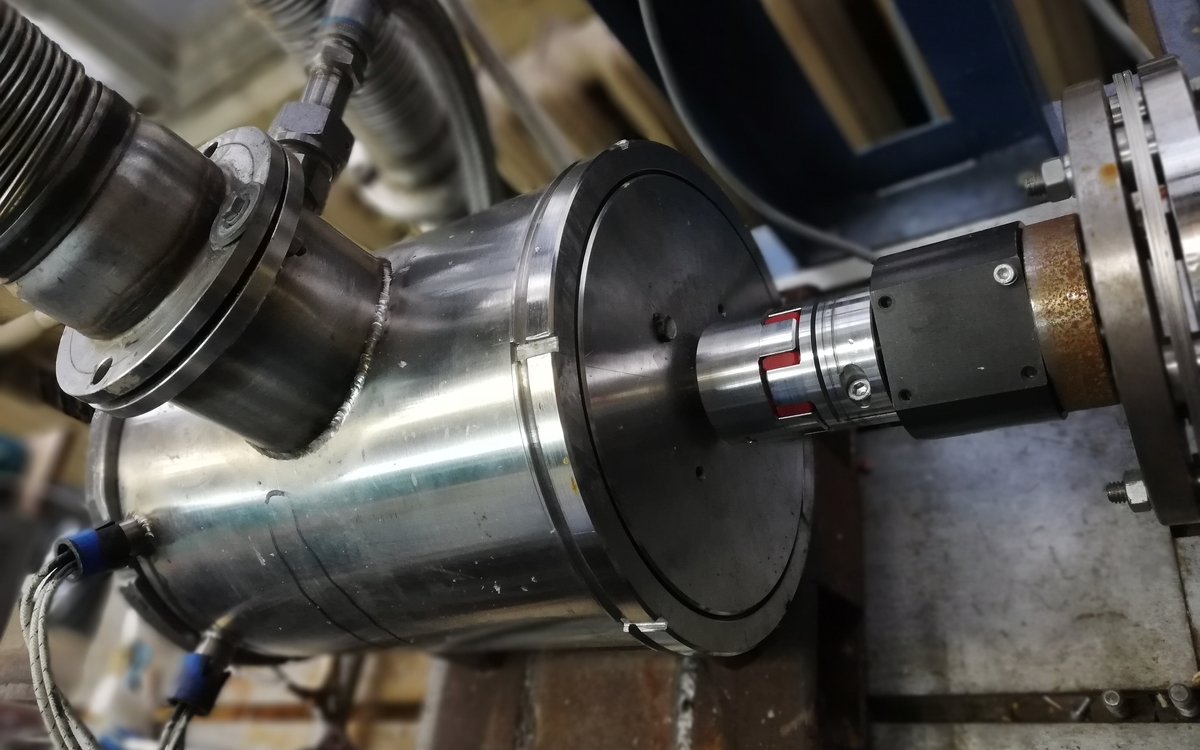
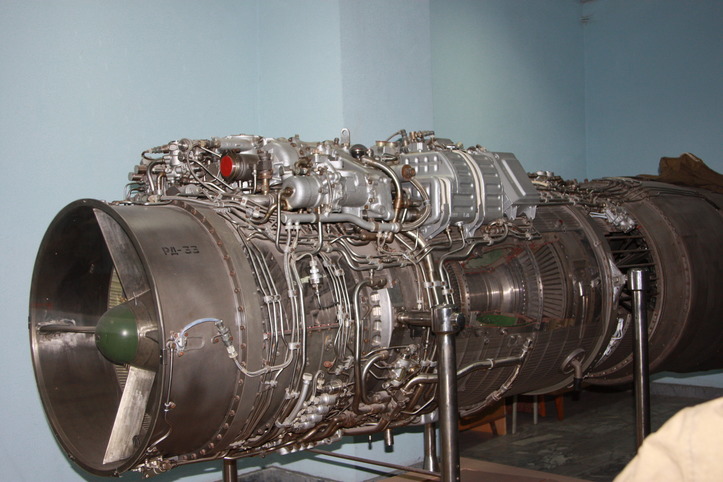
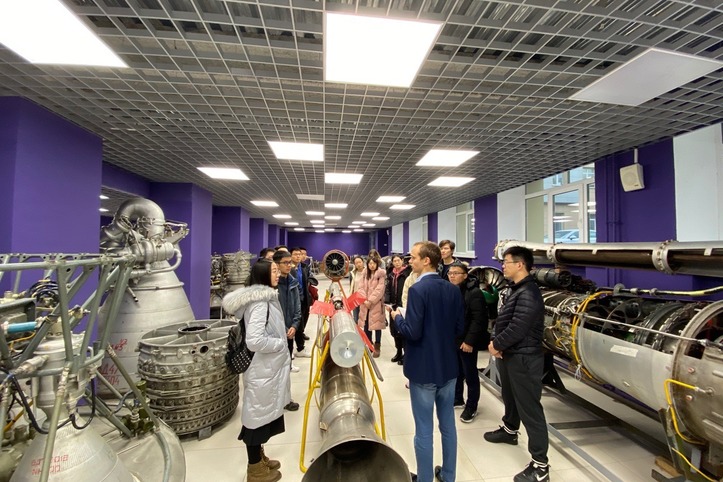
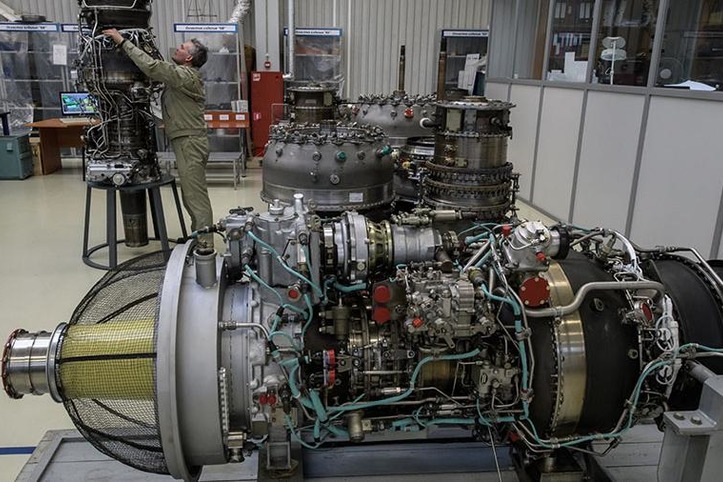
Or you can write to us using the form below
MAI uses cookies. Continuing to work with mai.ru , you confirm the use of your browser cookies by the site, which help us to make this site more convenient for users. However, you can prevent the storage of cookies in your browser settings.